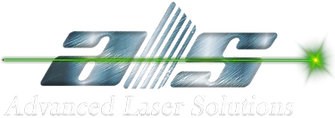

Laser Marking
Laser marking is a process that uses a concentrated beam of light to create permanent marks on the surfaces of target components. This technique employs focused laser beams to create easy-to-read, damage-free marks. Instead of using physical tools for etching surfaces, laser marking allows engineers and manufacturers to create numbers, images, or characters without compromising part quality. It’s a very versatile process, encompassing different techniques such as engraving, etching, foaming, carbon migration, etc.
Industrial laser marking is recognized as a versatile and precise technology for labeling, coding, and engraving a wide range of materials in various industrial sectors. This “non-contact” marking method is permanent and offers numerous advantages over traditional techniques such as ink printing or microdot mechanical engraving. Laser marking is widely adopted in sectors such as electronics, automotive, medical, and home appliances for its ability to create high-quality and durable markings on different materials.
There are two primary methods commonly employed in laser marking: pulsed laser marking and continuous wave (CW) laser marking.
Pulsed laser marking operates by delivering laser energy in intermittent pulses, with precise control over pulse duration and frequency. This modulation of energy allows for controlled heating and melting of the material, resulting in precise marks with minimal distortion. Pulsed lasers are great for avoiding heat-related problems and, since they’re not continually operating, they’re great for marking without damaging the product.
On the other hand, CW laser marking operates by delivering a continuous beam of laser energy to the workpiece, maintaining a constant energy output throughout the marking process. This continuous delivery of energy ensures consistent heating and melting of the material, resulting in stable and uniform marks. CW lasers can work for extended periods, but depending on what you’re working with, this can develop heat-related problems.
In conclusion, industrial laser marking, with its pulse and CW variants, offers a highly efficient, precise, and eco-friendly alternative to traditional marking methods. It’s a testament to how far we’ve come in harnessing the power of light for industrial applications.
Advantages of Pulse Laser Marking:
Customization: Pulse laser marking allows for customizable settings, including pulse duration and power, to suit specific materials and mark types.
Precision: By adjusting the pulse duration and power, operators can precisely control the depth and delicacy of the mark, from bold and deep to delicate and subtle.
Versatility: Pulse laser marking is adaptable to a wide range of materials. Metals require short, powerful bursts for deep marks, while ceramics and glass need longer, gentler pulses for more delicate markings.
Advantages of CW Laser Marking:
Efficiency: CW lasers provide a continuous and consistent beam, making them highly efficient for marking applications, especially when combined with computer-controlled systems for precise and rapid marking.
Power: These lasers can deliver high power outputs, making them suitable for deep and permanent marks on a range of materials, including metals and alloys.
Speed: CW lasers can mark at high speeds, making them ideal for high-volume production environments.
Pulse Laser Marking Applications:
Medical Device Marking: In the medical field, pulse laser marking is used to etch unique identifiers, logos, and critical data onto surgical instruments and medical devices.
Electronics Component Marking: Pulse lasers are ideal for marking tiny electronic components, such as microchips and circuit boards without damaging the sensitive electronics.
CW Laser Marking Applications:
Automotive Industry: CW laser marking is widely used in the automotive industry for permanent marking and identification of vehicle parts.
Aerospace and Aviation: CW laser marking plays a crucial role in the aerospace industry. Markings made with CW lasers are highly durable and can withstand high temperatures, pressure differentials, and harsh chemicals.
