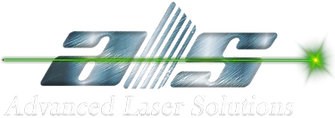

Laser Welding
Industrial laser welding is a highly precise and efficient welding technique used in various industries for joining metals with exceptional accuracy. It uses a high-energy laser beam to fuse metals together, creating a strong metallurgical bond. As the energy from the laser beam is absorbed by the surface, the heat causes the surface to melt, forming a molten pool that resolidifies in a few milliseconds. This process results in very narrow and precise welds, with minimal heat-affected zones (HAZ) and distortion.
Laser welding is not only used to weld metals like aluminum, copper, and stainless steel, but also other types of materials, including certain types of thermoplastics, glasses, and composites. It has found numerous applications across most industries, particularly in the automation of small-component welding, where tight control means there’s no need for cleanup. This is most useful in the automotive, aerospace, and electronics sectors, where precision and efficiency are the biggest driving factors.
There are two primary methods commonly employed in laser welding: pulsed laser welding and continuous wave (CW) laser welding.
Pulsed laser welding operates by delivering laser energy in intermittent pulses, with precise control over pulse duration and frequency. This modulation of energy allows for controlled heating and melting of the material, resulting in precise welds with minimal distortion. Pulsed lasers are great for spot and seam welding or biological sample testing, where heat input is a significant factor.
On the other hand, CW laser welding operates by delivering a continuous beam of laser energy to the workpiece, maintaining a constant energy output throughout the welding process. This continuous delivery of energy ensures consistent heating and melting of the material, resulting in stable and uniform welds. CW lasers are an excellent option for high-speed seam welding tasks like pressure sensors, airbag initiators, and battery tabs.
In conclusion, industrial laser welding, with its pulse and CW variants, offers a highly efficient, precise, and eco-friendly alternative to traditional welding methods. It’s a testament to how far we’ve come in harnessing the power of light for industrial applications.
Advantages of Pulse Laser Welding:
Precise Control: Pulse laser welding machines allow for precise control over the heat input, which is critical for preventing damage to delicate parts.
High Quality Welds: Pulse laser welding technology offers high-quality welds with minimal heat-affected zones.
Versatility: Pulse lasers can be used to weld a wide range of materials, including metals, plastics, and ceramics.
Advantages of CW Laser Welding:
Steady Energy Source: One significant advantage of CW lasers is their ability to deliver a constant power output over an extended period. This makes them ideal for applications that require a steady source of energy, such as deep penetration welding.
Simplicity: CW lasers tend to be simpler in terms of control, as the main requirement is to maintain a stable output.
Pulse Laser Welding Applications:
Precision Micro-Welding
Medical Device Manufacturing
Automotive Electronics
Battery Welding
Solar Panel Manufacturing
CW Laser Welding Applications:
Deep Penetration Welding
Shipbuilding
Aerospace Manufacturing
Automotive Assembly
Heavy Industry
